عیوب جوشکاری (welding defects) به مجموعه نقایص جوش گفته می شود که در ظاهر و کیفیت جوش تاثیر گذار است.
بعضی از این نقایص با ویژوال تست (بازرسی چشمی) قابل تشخیص، و برخی دیگر فقط با انواع تستهای غیر مخرب و مخرب شناسایی میگردد.
در اینجا به بررسی برخی از این عیوب میپردازیم:
1.روی هم افتادگی (انباشتگی جوش در کنارهها overlap or over-roll )
نقصی در کنار یا ریشه جوش است که به علت جاری شدن فلز بر روی سطح فلز پایه ایجاد می شود بدون اینکه ذوب و جوش خوردن با آن ایجاد شود. علت:
- حرکت کمتر از حالت نرمال یا طبیعی
- زاویه نادرست الکترود
- استفاده از الکترود با قطر بالا
- آمپراژ خیلی کم
نتیجه:
عوامل فوق کاری مانند بریدگی کناره دارد و یک منطقه تمرکز تنش از فلز جوش ترکیب نشده ایجاد میکند.
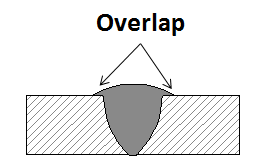
2. سوختگی یا بریدگی کناره جوش Undercut
شیاری در کنار یا لبه جوش که بر سطح جوش و یا بر فلز جوشی که قبلا را سبب شده است قرار دارد.
علت:
- آمپر زیاد
- طول قوس زیاد
- حرکت موجی زیاد الکترود
- سرعت بسیار زیاد حرکت جوشکاری
- زاویه الکترود خیلی به سطح اتصال متمایل بوده است.
- سرباره با ویسکوزیته زیاد
نتیجه:
عوامل فوق موجب یک منطقه تمرکز و یک منطقه مستعد برای ایجاد ترک خستگی میشود.
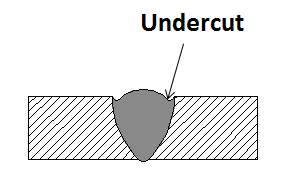
3. آخالهای سرباره Slag inclusion
به هر ماده غیر فلزی که در یک اتصال جوش بوجود میآید آخالهای سرباره میگویند؛ این آخالها میتوانند در رسوب جوش نقاط ضعیفی ایجاد کنند.
علت:
- پاک نشدن مناسب سرباره از پاسهای قبلی
- آمپراژ ناکافی
- زاویه یا اندازه الکترود نادرست
- آماده سازی غلط
نتیجه:
آخالهای سرباره استحکام سطح مقطع جوش را کاهش میدهند و یک منطقه مستعد ترک ایجاد میکنند.
4. ذوب ناقص (L.O.F) (Lack of fusion )
عدم اتصال بین فلز جوش و فلز پایه یا بین پاسهای جوش
علت:
استفاده از الکترودهای کوچک برای فولاد ضخیم و سرد
- آمپراژ ناکافی
- زاویه الکترود نامناسب
- سرعت حرکت بسیار زیاد
- سطح کثیف (پوسته نورد ، لکه ، روغن و … )
نتیجه:
اتصال جوش ضعیف میماند و به یک منطقه مستعد ایجاد خستگی تبدیل میشود.
5. تخلخل Porosity
تخلخل یا پروسیتی از مهمترین و شایع ترین عیوب جوش است. سوراخ یا حفرهای است که به صورت داخلی یا خارجی در جوش دیده میشود. تخلخل میتواند از الکترود مرطوب ، الکترود روکش شکسته یا از ناخالصی روی فلز پایه ایجاد شود. همچنین به نامهای (مک لولهای) ، (مک سطحی) و (سوراخهای کرمی) نیز شناخته میشود.
سایر علتها:
- سطح فلز پایه آلوده مثل آلودگیهای روغن ، غبار ، لکه یا زنگار
- مرطوب بودن روکش الکترود
- محافظت گازی ناکافی قوس
- فلزات پایه با مقادیر بالای گوگرد و فسفر
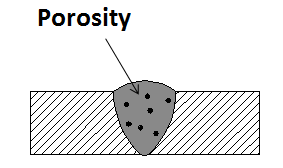
نتیجه :
به شدت استحکام اتصال جوش شده را کاهش میدهد. تخلخل سطحی به اتمسفر خورنده اجازه میدهد که فلز جوش را مورد حمله قرار دهد و موجب نقص در آن شود.
6. همراستا نبودن اتصال جوش Join misalignment
این مشکل معمولا همراستا و همسطح نبودن قطعاتی که به هم جوش میشوند نامیده میشوند. عدم همراستایی یک مشکل معمول در آماده سازی روشهای لب به لب و فیتاپ لوله است و هنگامی ایجاد میشود که صفحات ریشه و صفحات اتصال از فلز پایه در محل درست خود برای جوشکاری قرار نگرفتهاند.
علت :
- مونتاژ نادرست قطعاتی که باید جوش شوند.
- خال جوشهای ناکافی که میشکند یا بست زدن ناکافی که موجب حرکت میشود.
نتیجه:
همراستا بودن جدی است، زیرا نقص در ذوب لبه ریشه موجب ایجاد مناطق تمرکز تنش میشود در سرویس دهی موجب شکست خستگی زودرس اتصال میشود.
7. نفوذ ناقص (L.O.P) Lack of penetration عدم نفوذ کامل فلز جوش به ریشه اتصال
علت:
- آمپر بسیار پائین
- فاصله ریشه ناکافی
- استفاده از الکترود با قطر بالا
- سرعت حرکت زیاد
نتیجه:
از عیوب جوشکاری که جوش را ضعیف میکند و به مستعد ایجاد خستگی تبدیل میشود.
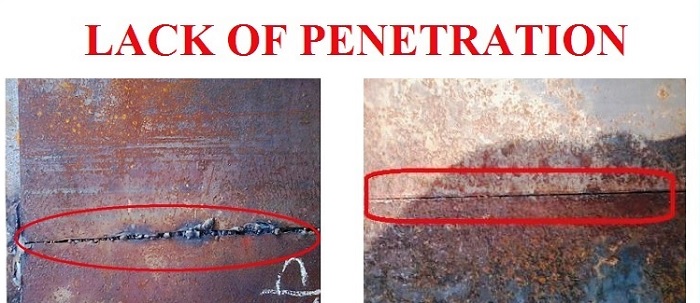
8. ترک جوش Weld cracking
انواع مختلفی از عدم اتصال ممکن است در جوش یا مناطقی که تحت تأثیر حرارت HAZ قرار میگیرند، رخ دهد. جوشها ممکن است دارای تخلخل ، آخالهای سرباره یا انواع ترکها باشند.
تخلخل و آخالهای سرباره شاید در جوش تا حدی قابل قبول باشد اما طبق استاندارد ترکها در جوش هرگز قابل قبول نمیباشند(بدون توجه به اندازه و مقدار آن). وجود ترک در جوش یا در مجاورت جوش نشانگر این مسئله میباشد که حتما مشکلی در حین کار وجود داشته است.
بررسی دقیق ترکها ، تعیین علت اجاد آنها و نیز راههای جلوگیری از آنها را برای ما امکان پذیر میسازد. در ابتدا ما باید به این مسئله توجه داشته باشیم که بین ترک و شکست تفاوت قائل شویم.
منظور ما از ترک ، پدیدهای است که در اثر عواملی مانند انجماد ، سرد شدن و تنشهای داخلی که به علت انقباض جوش میباشد ایجاد میگردد. ترکهای گرم ، ترکهایی میباشند که در دماهای بالا رخ میدهند و معمولا به انجماد ربط دارند.
ترکهای سرد ترکهایی هستند که بعد از اینکه جوش به دمای اطاق رسید، رخ دهد و ممکن است حتی به HAZ ربط داشته باشد.
بیشتر ترکها در اثر تنشهای فیزیکی انقباض که معمولا با کشیدن یا تغییر شکل جسم همراهی باشد در هنگام سرد شدن جوش رخ میدهد، ایجاد میشوند، اگر انقباض محدود شود، این تنشهای فیزیکی کرنشی ، تنش داخلی پسماند را بوجود میآورند که این تنشهای پسماند منجر به ایجاد ترک میشوند.
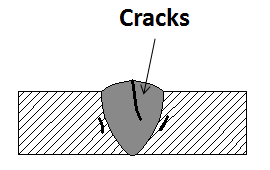
ترک مرکزی :
ترک به صورت خط مرکزی در مرکز یک پاس جوش معین قرار دارد. اگر انتهایی پاس جوش داشته باشیم و اینپالیدرمرکز اتصال باشد آنگاه این ترک مرکزی در مرکزاتصال نیز رار خواهد داشت.
در مورد پاس های چند تای که چندین پاس در هر لایه وجود دارد ترک مرکزی از نظر هندسیب ممکن است در مرکز اتصال قرار نداشته باشد. ار چه اغلب دیده می شود که در مرکزاتصال قرار دارد. علت ترک مرکزی یکی از سه پدیده زیر می باشد:
ترکی که ناشی از جدایش و تفکیک باشد.
ترکی که مربوط به شکل گرده جوش میباشد.
ترکی که مربوط به تغییرات سطحی میباشد.
متأسفانه تمام سه پدیده فوق خودشان را در قالب یک نوع آشکار میکنند و تشخیص دادن ترک مشکل میباشد. علاوه بر این ، تجربهها نشان دادهاند که اغلب 2 یا حتی 3 پدیده فوق با یکدیگر برهمکنش داده و در ایجاد ترک مؤثرند.
در واقع درک مکانیسم اصلی هر یک از انواع ترکهای مرکزی به ما کمک میکنند تا به دنبال راه حلی برای از بین بردن ترک باشیم.
ترک مرکزی ناشی از جدایش این ترکها وقتی رخ میدهد که ترکیباتی با نقطه ذوب پایین نظیر فسفر ، روی ، مس و گوگرد در نقاط خاصی در حین فرآیند سرد شدن جدایش یابند.
در حین فرآیند انجماد ، ترکیباتی با نقطه ذوب پایین در فلز مذاب به نواحی مرکزی اتصال رانده میشود چون آنها تا آخرین ترکیباتی هستند که شروع به انجماد میکنند و جوش در این نواحی تمایل به تفکیک و جدایش مییابد.
در جوشکاری میتوان از الکترودهایی با مقادیر بالای منگنز استفاده تا بتوانیم بر تشکیل سولفید آهن با نقطه ذوب پایین غلبه کنیم. متأسفانه این مفهوم نمیتواند برای مواد غیر فرار دیگری بجز گوگرد بکار رود.
ترک مرکزی ناشی از شکل گرده جوش
نوع دوم ترک مرکزی ، ترک ایجاد شده در اثر شکل پالس جوش میباشد، این ترک در فرآیندهایی که همراه با نفوذ عمیق میباشند نظیر فرآیند FCAW , SAWتحت محافظ CO2 دیده میشود.
وقتی که یک پالس جوشکاری دارای عمق بیشتری نسبت به هضم آن جوش (در نمای سطح مقطع) باشد. برای رفع این نوع ترک ، پالسهای جوش باید دارای عرضی حداقل برابر با عمق باشد.
توصیه میشود که نسبت پهنای جوش به عمق آن برابر با 1 به 14/1 به 1 باشد تا این نوع ترک رفع شود. اگر از پالسهای چندتایی استفاده شود هر پاس دارای پهنای نبت به عمق آن باشد، یک جوش فاقد ترک خواهیم داشت.
وقتی که یک ترک مرکزی بخار شکل پاس تحت بررسی است، تنها راه حل این است که نسبت پهنای جوش به عمق آنرا تغییر دهیم. این موضوع شاید در برگیرنده آن باشد که تغییری در طراحی اتصالها داشته باشیم.
از آنجایی که عمق جوش تابعی از نفوذ میباشد شاید مفید باشد که مقدار نفوذ را کاهش دهیم بدین منظور میتوانیم از آمپرهای پایینتر و الکترودهایی با قطرهای بالاتر استفاده کنیم. راهکارهای فوق دانسیته جریان را کاهش میدهد و مقدار نفوذ را محدود میکند.
ترک مرکزی ناشی از شرایط سطحی جوش
آخرین مکانیسمی که سبب ایجاد ترک مرکزی میباشد تغییر شرایط سطحی میباشد.
وقتی جوشهایی با سطح مقعر ایجاد میشود تنشهای ناشی از انقباضهای داخلی موجب میشود که سطح جوش کشیده شود.
برعکس وقتی که سطح جوش محدب باشد نیروی ناشی از انقباضهای درونی موجب میشود که سطح جوش فشرده میشود.
سطح جوش مقعر ، اغلب ناشی از ولتاژهای بالای قوس میباشد. کمی کاهش در ولتاژ قوس موجب میشود که گرده جوش به حالت محدب تغییر شکل دهد و تمایل به ترک حذف گردد.
سرعتهای حرکت بالا نیز ممکن است به این موضوع کمک کند و کاهش در سرعت حرکت جوشکاری ، مقدار پراکندگی توسط جوش را افزایش میدهد و سطح جوش به صورت محدب تغییر حالت میدهد.
جوشکاری در حالت قائم سر پایین باعث ایجاد این نوع ترک میشود. جوشکاری در حالت قائم رو به بالا میتواند از بروز این نوع ترک جلوگیری نماید.
ترک منطقه متأثر از جوش
ترک منطقه متاثر از جوش (HAZ) بوسیله جدایشی که بلافاصله مجاور گرده جوش رخ میدهد مشخص میشود، اگر چه این نوع ترک مربوط به فرآیند جوشکاری میباشد با این حال ترکی است که در روی پایه رخ میدهد نه درخود جوش.
این ترک به نام تک مجاور جوش ، ترک گوشهای یا ترک تأخیری نیز نامیده میشود. چون این ترک بعد از اینکه فولاد در دمای f ْ400 انجماد یافته است رخ میدهد ترک انجمادی نیز نامیده میشود و چون با هیدروژن نیز همراه میباشد ترک همراه با هیدروژن نیز نامیده میشود.
برای اینکه ترک HAZ رخ دهد سه شرط باید بطور همزمان برقرار باشد:
- باید مقدار کافی هیدروژن وجود داشته باشد.
- جوش باید به حد کافی نفوذ پذیر باشد.
- باید به حد کافی تنشهای داخلی یا پسماند وجود داشته باشد.
حذف یکی از سه شرط فوق معمولا باعث میشود که این نوع ترک از بین برود. در جوشکاری ، یک راه برای حذف این نوع ترک این است که دو یا سه متغیر (مقدار جوش نفوذ پذیر جوش) را محدود کنیم.
هیدروژن از منابع مختلفی میتواند وارد جوش شد. رطوبت و ترکیبات آلی منابع اصلی هیدروژن در جوش میباشند. هیدروژن میتواند در فولاد ، الکترود ، ترکییبات روپوش الکترود و در آتمسفر وجود داشته باشد.
ترک عرضی
ترک عرضی ترک متقاطع نیز نامیده میشود. ترکی است که در جهت عمود بر طول جوش ایجاد میشود. این نوع ترک از انواعی است که اغلب در جوشکاری با آن مواجه میشویم و معمولا جوشی که دارای استحکام بالاتری در مقایسه با فلز پایه میباشد دیده میشود.
این نوع ترک میتواند همراه با هیدروژن نیز باشد و کل ترک منطقه متأثر از جوش HAZ که پیشتر شرح داده شد ناشی از مقدار بالای هیدروژن ، تنشهای پسماند و ریز ساختارهای حساس میباشد.
فرق عمده بین این دو ترک این میباشد که ترک عرضی در فلز جوش نتیجه تنش پسماند طولی میباشد. چنانچه پاس جوشکاری بصورت طولی انقباض یابد، فلز پایه در مقابل این نیرو مقاومت میکند و در واقع دچار تراکم و فشردگی میشود.
استحکام بالای فلز پایهای که در مجاورت جوش میباشد در برابر فشردگی ناشی از انقباض جوش مقاومت میکند و در واقع فشرده شدن جوش را محدود میکند. بخاطر ممانعتی که فلز پایه به عمل میآورد، تنشهای طولی در جوش گسترش مییابد. وقتی با ترکهای عرضی مواجه میشویم باید سطح هیدروژن و شرایط نگهداری الکترودها را مد نظر داشته باشیم.
در مورد ترک عرضی ، کاهش استحکام فلز جوش معمولا یکی از راهکارهای حذف این نوع ترک میباشد. تأکید زیادی بر روی فلز جوش وجود دارد چون فلز پر کننده به تنهایی ممکن است جوشی رسوب دهد که دارای استحکام پایینتری باشد و نیز تحت شرایط عادی فلزی نرم باشد.
البته با تأثیر عناصر آلیاژی استحکام جوش بالا میرود و از نرمی آن کاسته میشود. استفاده از جوشهایی با استحکام پایینتر ، یک راه حل مؤثر در کاهش ترک عرضی مؤثر میباشد، البته به شریطی که استحکام جوش با استانداردهای تعریف شده مطابقت داشته باشد.
9. پیچیدگی
پیچیدگی یا اعوجاج تا حدی در تمام انواع جوشکاری وجود دارد، در بسیاری موارد آنقدر کوچک است که به سختی قابل رؤیت است، ولی در بعضی موارد باید پیش از جوشکاری به اعوجاجی که متعاقبا ایجاد میشود توجه کرد. مطالعه و بررسی اعوجاج بسیار پیچیده است و آنچه در ادامه آمده خلاصه است:
علل اعوجاج هنگامی که فلز تحت بار ، کرنش میکند یا حرکت میکند و تغییر شکل میدهد: تحت بار گذاری ضعیف فلزات بصورت الاستیک باقی میمانند. (به شکل اصلی خود باز میگردند یا پس از اینکه بار برداشته شد شکل میگیرند) که این تحت عنوان محدوده الاستیک شناخته میشود.
تحت بار خیلی زیاد ، فلزات تا حدی تحت تنش قرار میگیرند که دیگر به شکل اول خود باز نمیگردند یا شکل نمیگیرند و این نقطه (نقطه تسلیم) نامیده میشود (تنش تسلیم).
فلزات با حرارت دیدن انبساط مییابند و وقتی سرد میشوند منقبض میشوند، فلزات در حین جوشکاری گرم و سرد میشوند که موجب تنشهای بالای ناگهانی و اعوجاج میشوند.
اگر این تنشهای زیاد از محدوده الاستیک بگذرند و از نقطه تسلیم نیز رد شوند، برخی پیچیدگیهای دائمی در فلز پدید میآید، تنش فلز در دمای بالا کاهش مییابد. اعوجاج اثر ناخواسته انبساط و انقباض فلز حرارت دیده است.
انواع پیچیدگی
سه نوع اصلی پیچیدگی وجود دارد:
کنترل پیچیدگی میتواند در سه مرحله انجام گیرد:
- – قبل از جوشکاری
- – حین جوشکاری
- – بعد از جوشکاری
کنترل پیچیدگی قبل از جوشکاری توسط روشهای زیر انجام میشود:
خال جوش زدن _ گیره و نگهدارنده _ پیشگرم کامل و سرتاسری _ مونتاژ اولیه مناسب
کنترل اعوجاج پس از جوشکاری:
سرد کردن آرام – صافکاری شعلهای (حرارت دهی معکوس) – آنیل کردن -تنش زدایی – نرمال کردن – صافکاری مکانیکی
در سازههای فلزی ساختمان معمولا روشهای 1و2 بیشتر اعمال میگردد و سایر روشها در کارهای صنعتی بیشتر کاربرد دارند.
آنیل کردن : یک پروسه عملیات حرارت است که برای نرم کردن فلزات جهت کل سرد یا ماشین کاری بکار میرود، قطعه یا کار نهائی معمولا در کوره تا دمای بحرانی (برای فولاد با 0.52% کربن حدود Cْ 820 – 723) )حرارت داده میشود و سپس به آرامی سرد میشود.
تنش زدایی (PWHT) : حرارت دهی یکنواخت قطعات جوش شده تا دمایی زیر دمای بحرانی است که با سرد کردن آرام دنبال میشود، این پروسه نقطه تسلیم فلز را کاهش میدهد، لذا تنشهای باقی مانده در قطعه کاهش مییابد.
نرمال کردن :پروسهای برای ریز کردن ساختار دانهای فلز است که موجب بهبود مقاومت آن در برابر شوک و خستگی میشود. در نرمال کردن قطعات جوش شده تا بالای دمای بحرانی( Cْ 820 برای فولاد با کربن25/0% (تقریبا یک ساعت برای هر 25 mm ضخامت حرارت میبیند و سپس در هوای محیط سرد میشود )
تجربیات خود را در رابطه با عیوب جوش و برطرف کردن آنها ، در نظرات، با ما در میان بگذارید…